Tasks and applications
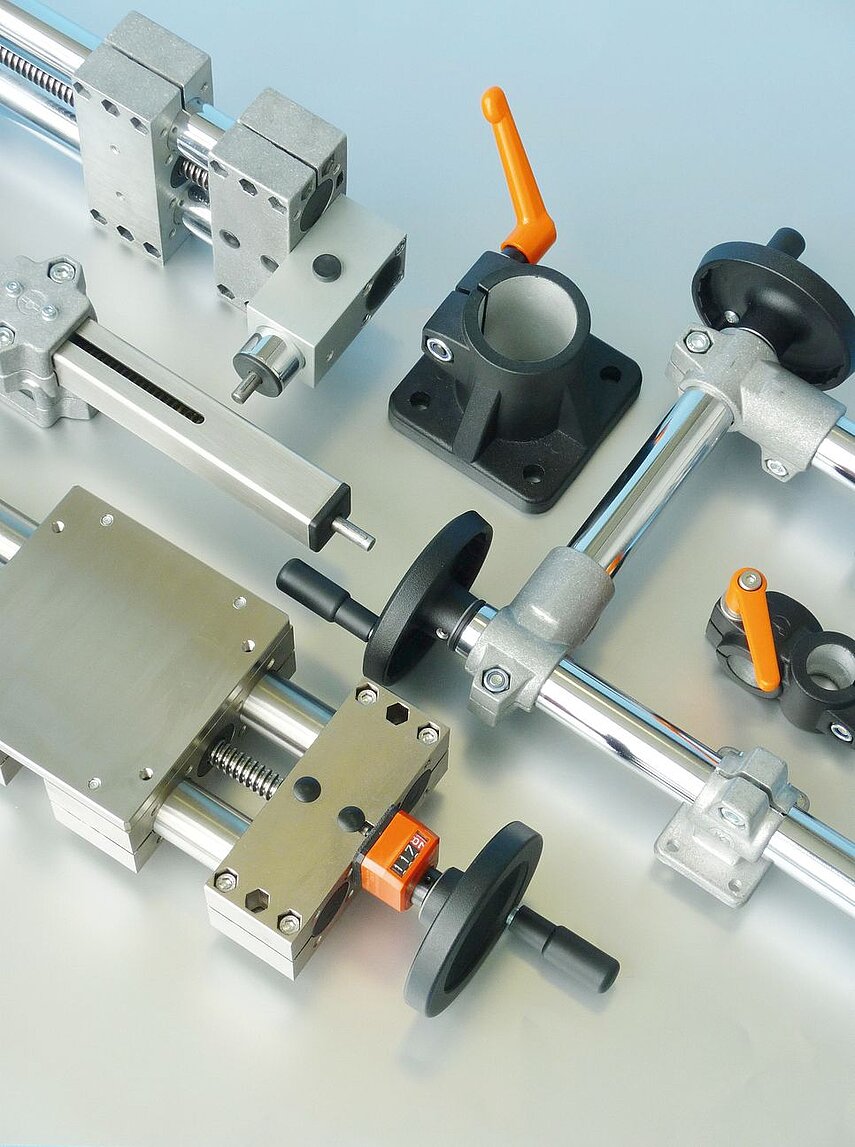
Guides in machine construction
A guide is a connection between two objects that only permits movement along one axis. Guides can be fitted with fixed or variable travel points. Combining multiple guides makes it possible to enforce defined movements within three-dimensional space.
Uses of guides
A guide moves an object exclusively along a defined axis. The guide determines not only the direction but also the speed, feed force, and stopping points along the desired direction. Only two degrees of freedom are possible per guide. These degrees of freedom may appear as follows, depending on the positioning:
- Forward and backward - Up and down - Left and right
- Radially clockwise or counterclockwise
Arbitrary stopping points can be defined long the guide path. This is accomplished with fixed or movable sensors or programmable control of servo motors and incremental encoders. Simple guides in machine construction, such as roller-guided conveyor systems, can define the desired stopping points by means of end stops or barriers. On the other hand, the driven object can itself be a guide system. This process can be continued as necessary to build up XYZ guides with high precision. In principle, however, fewer axes of movement make a guide firmer. Special design measures are required for hanging or standing guides, such as form-fitting sliding blocks.
Guides in machines must always function precisely and reliably. Depending on the application, a deviation from the defined direction can lead to significant quality impairments in the product. This is especially true of CNC machine tools and 3D coordinate measurement instruments. Other requirements include:
- Unimpeded movement
- Acceptance of large forces
- Cost-effective design
Applications of guides in machine construction
Typical uses for guides in machine construction include the following applications:
- Pick-and-place systems
- CNC machine tools, especially mills
- 3D coordinate measurement systems
- 3D printers
- Infeed and outfeed systems for unfinished or finished products in processing machinery
- Inhouse transport of unfinished, finished, or packaged products or containers
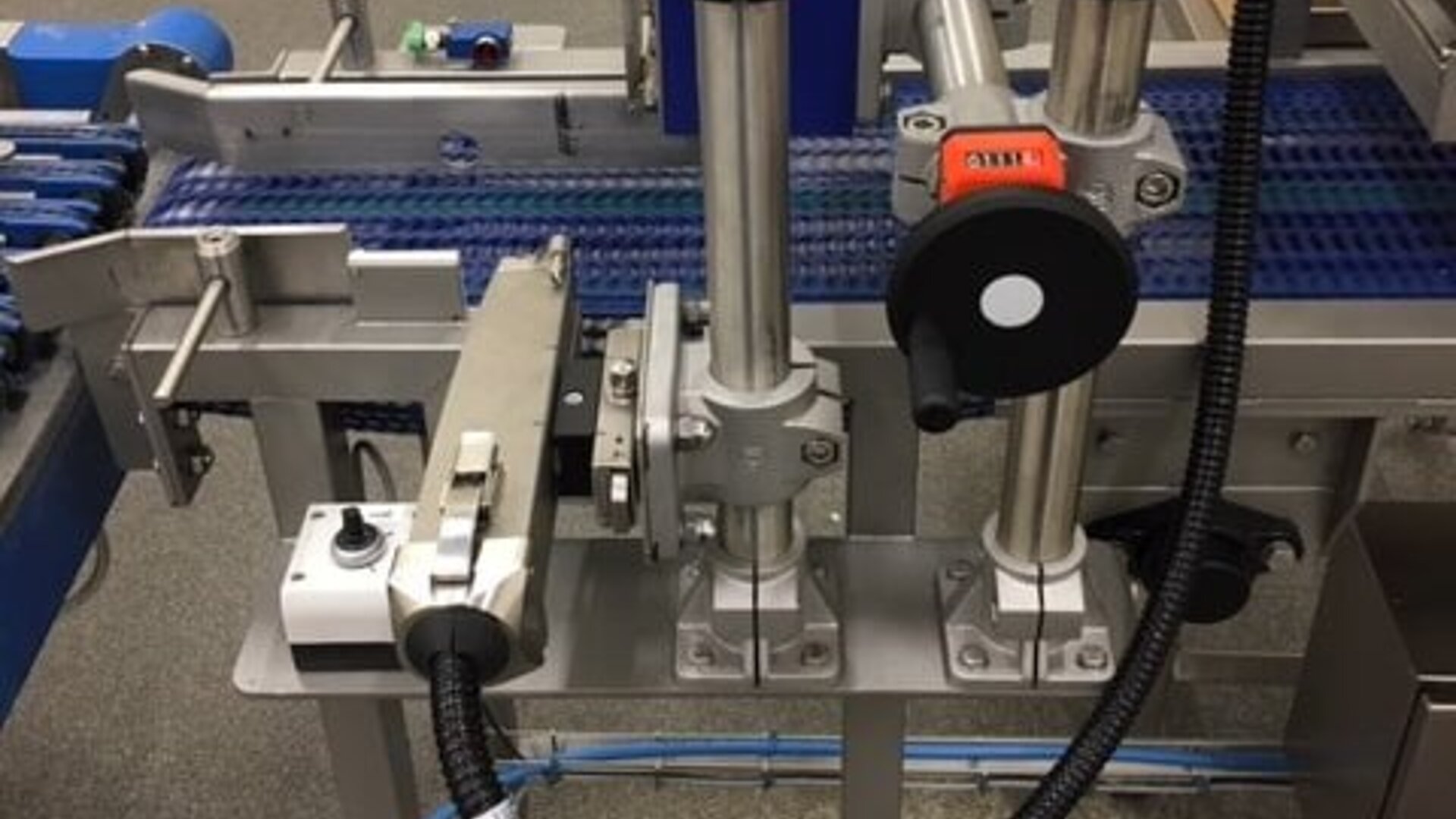
What kinds of guides are there?
Experts distinguish primarily between roller and plain bearing guides. Roller-guided systems make use of rollers to support the guide element or track. These systems are not braked and can use gravity or added acceleration to move the products.
Plain bearing guides make use of oil or grease lubrication, air cushions or repelling magnetic forces.
A guide is always associated with a motive actuator. This could be a hydraulic, pneumatic, or electromagnetic linear motor or a radial drive with spindle or gear rack.
The type of guide is determined based on the specific application. Roller-guided systems require lower driving forces. They can utilize gravity and may be designed without a guide element. On the other hand, they become easily soiled and are expensive due to the many components involved.
Plain bearing guides are self-braking in the event of a power loss. They must overcome high levels of friction at startup and require equally high acceleration forces. The drive system of the plain bearing guide must take this into account. They are especially compact and simple in design. The combination of guide rail and enclosing sliding block make these types of guide very safe. The glide film, consisting of lubricant, compressed air or repelling magnetic forces, provides damping effects. As a result, plain bearing guides offer particularly smooth movement as long as the startup impulse is under control. The impulse damping can be achieved with a gear rack, spindle or chain drive, for example. These drive types have force-attenuating properties that make them optimal for driving plain bearing guides.
Contact
Do you have any special challenges in the field of research and development? Contact us. We look forward to your inquiry and will help you find just the right solution for your application.